How to Wipe Out Orange Peel During Electrostatic Powder Painting
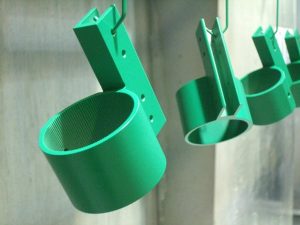
Achieving the right amount of electrostatic powder paint on the part is very important for durability reasons as well as eliminating orange peel. If you spray too little powder on the part, you will most likely end up with a grainy texture to the powder also known as “tight orange peel.” This is because there was not enough powder on the part for it to flow-out and create a uniform coating. Besides the poor aesthetics of this, the part will likely start to rust or oxidize in these areas because air is allowed to contact the bare metal still. Using an LED flashlight is the east way to overcome this.
If you spray too much powder on the part, you will most likely end up with large wavy orange peel. The excessive thickness of the powder will also make the part more prone to chipping.
Achieving the perfect powder thickness, not too light and not too heavy will take some practice. Make sure to take note of any orange peel you get and keep in mind that you need to shoot the next part heavier or lighter. I have found a somewhat reliable method of keeping an LED flashlight on the part the entire time that I am spraying. As soon as the flashlight no longer reveals bare metal in a spot, that is the perfect amount of powder and I do not spray any more powder.
A more reliable and scientific approach to this is measuring the thickness of the powder with a Mil Thickness Gauge. This can only be done after the powder is cured in the oven. If you are serious about powder coating, I strongly recommend adding this tool to your collection. If you are powder coating for customers, I would say it is a requirement. The price of these has come down drastically over the past couple of years and it will allow you to read the thickness of a coating. It is best to get one that works on ferrous (steel, iron) and non-ferrous (aluminum, magnesium) metals. This mil thickness gauge reads both and it also has v-groove probes which allows you to make your readings on curved parts.To use this properly, you would shoot a part as you normally would, cure it in the oven, and then read the thickness. All powers will have a recommended mil thickness range usually between 2.0 to 3.0 mils. As long as the mil-thickness you read falls into the range, the part has the right amount of powder on it. If it is too little or too much, make the necessary adjustments the next time you powder coat. This is the best and fastest way to learn how much powder needs to be applied.
Extra Tip: To achieve mirror-like coating, completely free of orange peel, I have had great success with this method, especially using gloss black.
1. Shoot the powder just like normal.
2. Put the part in the oven and set the temp to 245 degrees F.
3. As soon as the powder looks wet, remove the part.
4. Immediately spray a very light coat, just enough to not see a reflection.
5. Insert the part back in the oven and do a full cure.
–Excerpt from powdercoatguide.com, if you have any doubt,please contact us to remove it.